The Pros and Cons of Precast Concrete
Ever feel like construction projects drag on forever? Enter precast concrete form, the time-saving superhero of the construction world El Paso Concrete Contractors. It's durable, versatile, and made to speed up builds. But is it necessarily your best choice?
Let’s break down its benefits and drawbacks. So you can decide if it’s right for your next project.
What’s Precast Concrete, Anyway?
Let's suppose you bake a cake. You mix the batter. Bake it in a controlled oven. And let it cool before bringing it to the party. That’s precast concrete in a nutshell.
It’s made in a factory using reusable molds. Then, it's cured under controlled conditions. And shipped to the site ready to install. Simple, right?
This method keeps things efficient and consistent. But like any recipe, it has its quirks. Let’s explore why precast concrete is both celebrated and critiqued.
The Perks of Precast Concrete
1. Fast Construction, No Waiting Around
Precast concrete is a timesaver’s dream. Forget waiting days or weeks for concrete to cure on-site. Precast elements are ready to go as soon as they arrive.
Rainstorms or freezing temperatures? No problem. The process moves forward without a hitch. For projects on tight deadlines, this efficiency is a huge plus.
2. Built to Last
Precast concrete isn’t just strong; it’s rock-solid. Made in controlled environments, it avoids the inconsistencies of on-site pours.
No surprise cracks or weak spots here. It is dependable. No-drama friend you can always count on. It’s why bridges, tunnels, and stadiums rely on precast elements.
3. Saves Money in the Long Run
Here’s where the precast gets practical. It might feel pricey upfront. But the long-term savings are undeniable.
Faster construction means less money spent on labor. Plus, factories churn out precast pieces efficiently, keeping production costs in check. Over the course of a big project, those savings add up fast.
4. Looks Good, Stays Consistent
Precast concrete is like a tailor-made suit. It fits perfectly and looks exactly how you want it to. Factories can create uniform pieces every time, whether it’s walls, beams, or staircases.
It’s also highly customizable—molds can shape it into almost anything, giving architects a lot of creative freedom.
5. Friendlier to the Planet
Construction often gets a bad rap for being wasteful, but precast concrete tries to change that. Factories use materials more efficiently, reducing waste.
Leftover concrete? It’s recycled. Plus, because precast requires fewer resources overall, its carbon footprint tends to be smaller than traditional methods.
6. Keeps Workers Safer
Construction sites are full of risks. Precast concrete is really a safer option. Much of the work happens off-site. They do it in a controlled setting.
This reduces the need for workers to handle potentially dangerous tasks on-site. For example, pouring concrete at dizzying heights. That kind of safety is a perk for workers. But we believe it’s a necessity.
7. Quiet, Clean, and Quick Installation
Nobody likes a noisy, disruptive construction site. Precast concrete keeps things tidy. No endless truckloads of gravel, no loud cement mixers.
Installation is faster and quieter, which is a big win in crowded cities or peaceful neighborhoods. Your project won’t make you the local villain.
The Challenges of Precast Concrete
1. It’s Heavy, Really Heavy
If precast concrete had a personality, it’d be the heavyweight champ. Moving those large, dense slabs requires special equipment.
From reinforced trucks to cranes. Transportation can be a logistical headache. Especially for remote locations. And let’s not forget the fuel costs. That comes with moving such massive loads.
2. Installation Needs Extra Planning
Precast concrete is precise, but that precision demands careful planning. Cranes and skilled operators are often needed to position pieces correctly.
Make a single mistake during installation. And it can throw off the entire project. Think of it as solving a puzzle. Every piece has to fit perfectly—or else.
3. Not Very Forgiving
Here’s the thing about the precast. It doesn’t do well with last-minute changes. Make a piece. And it’s set in stone (literally).
Is the design change or measurement off? Then, you’re looking at costly delays to reorder or refabricate. Flexibility is not its strong suit.
4. Steep Upfront Costs
Precast concrete production involves a lot of upfront investment. The molds, specialized equipment, and factory setup don’t come cheap. While it often pays off in the long run, smaller projects might struggle to justify the initial expense.
Precast vs. Cast-In-Place: A Quick Face-Off
Precast concrete is like a fast and reliable car. That gets you from A to B in record time. While cast-in-place concrete is more like a custom-built vehicle. It takes longer to assemble. But offers flexibility to adapt to last-minute tweaks.
So, how do you choose? If you value speed, consistency, and durability, precast is your go-to. But does your project need on-the-fly changes? Or you’re working on a smaller scale? Cast-in-place might make more sense.
Interesting Facts and Stats about Precast Concrete
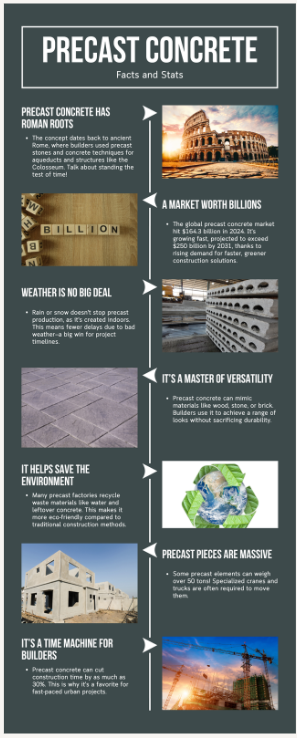
Final Thoughts: Is Precast Concrete Right for You?
Precast concrete is a great choice for modern construction. It’s quick and strong. Plus, it is eco-friendly. That makes it a favorite for large-scale projects. But it’s not without its quirks. Transportation challenges. High upfront costs. And limited flexibility. These all can be stumbling blocks.
Are you building a skyscraper? Or a stadium? Precast concrete offers plenty of advantages. But, it works best in the right hands. Like any other tool. Do proper planning and execution. And it can help create structures that stand tall for decades.
Ready to embrace precast concrete? It just might be the building block your next project needs. Call us today to learn more!

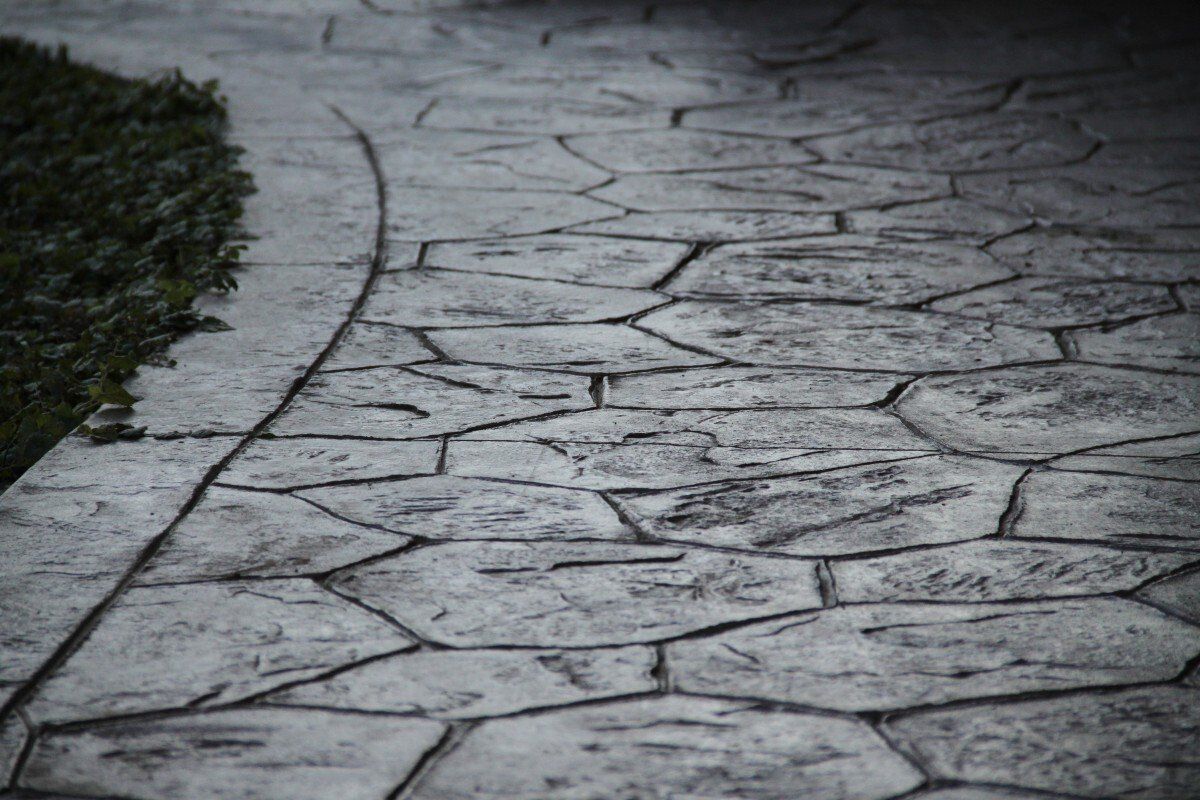
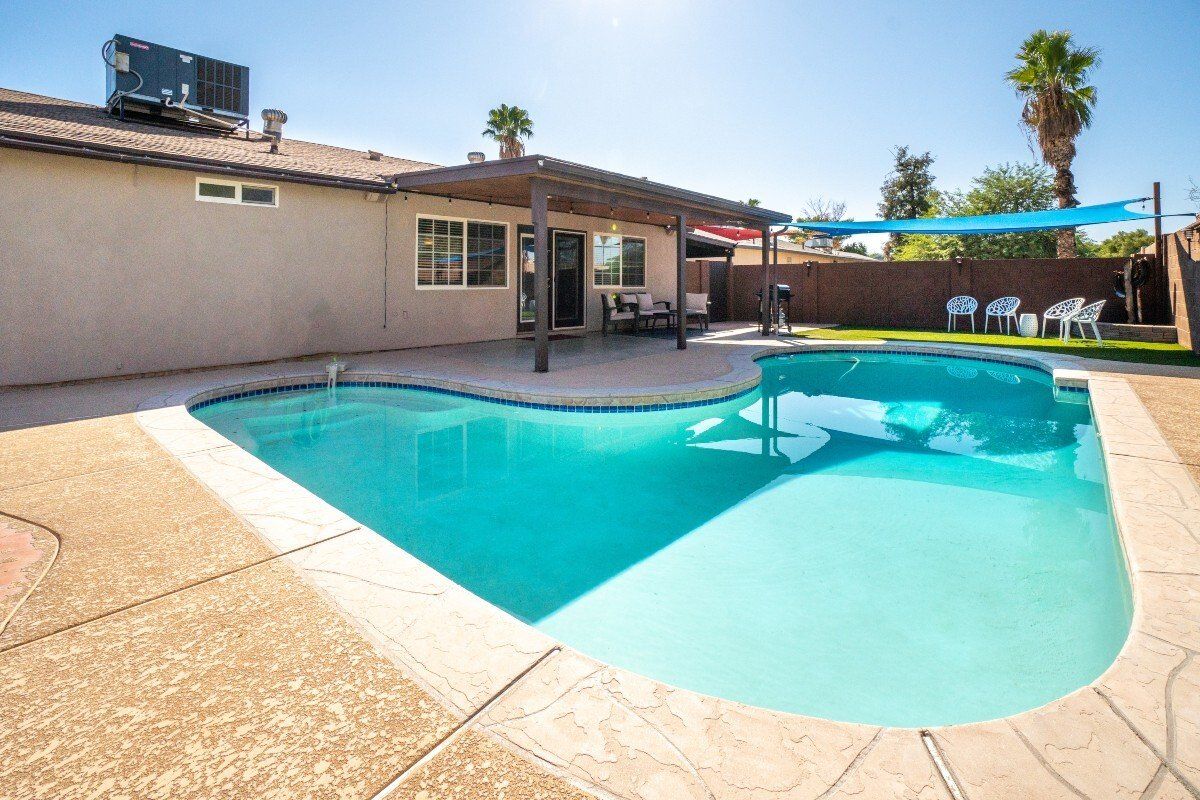
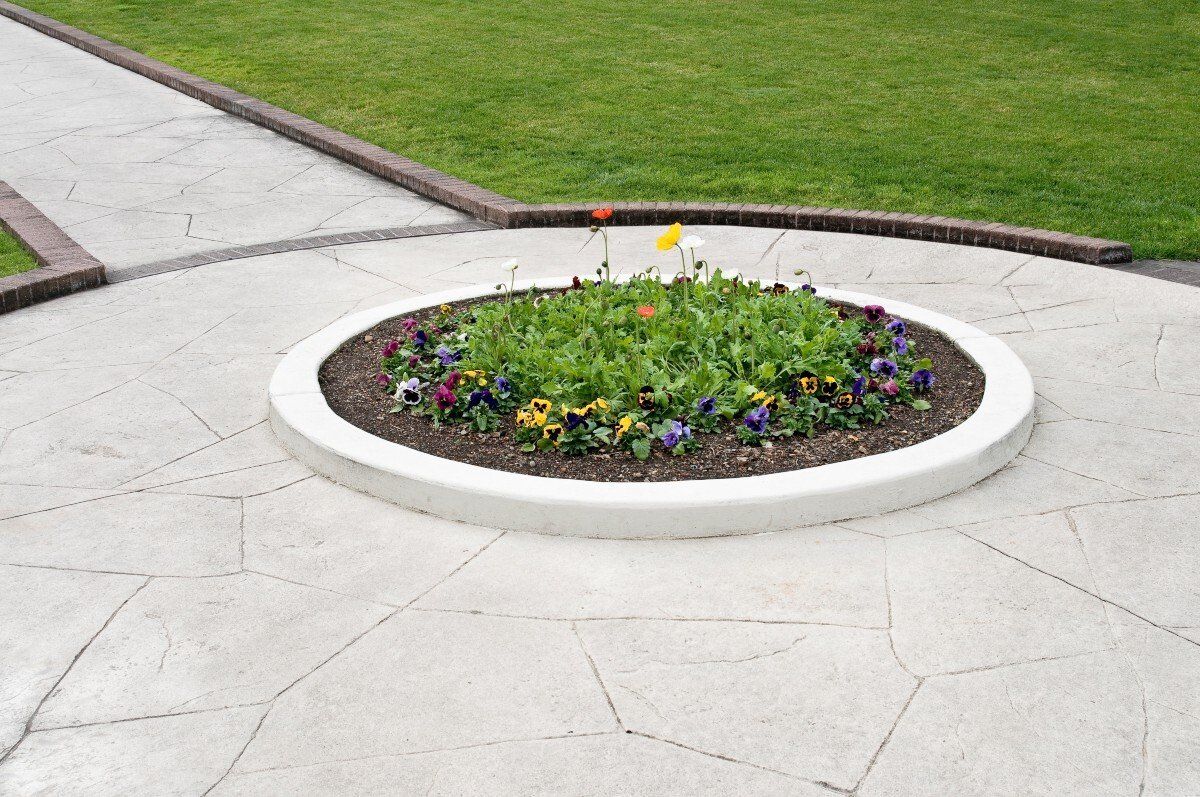